The Ultimate Guide to House Framing in Canada: A Comprehensive Look at LG Construction’s Approach
Framing is the backbone of any home. It is the structural framework upon which walls, floors, and roofs rest, forming the essential shape and strength of a house. In Canada, where the weather can be unforgiving, ensuring that a home’s frame is strong and resilient is crucial to its longevity and performance. LG Construction, a premier player in the Canadian home-building sector, excels in delivering top-tier framing services for custom homes.
This blog offers a detailed and expansive guide to the entire process of house framing in Canada, focusing on how LG Construction executes each stage of the process. Whether you’re a future homeowner curious about the framing of your new home or someone with a professional interest, this guide will take you step by step through the nuances of building a frame that will stand the test of time.
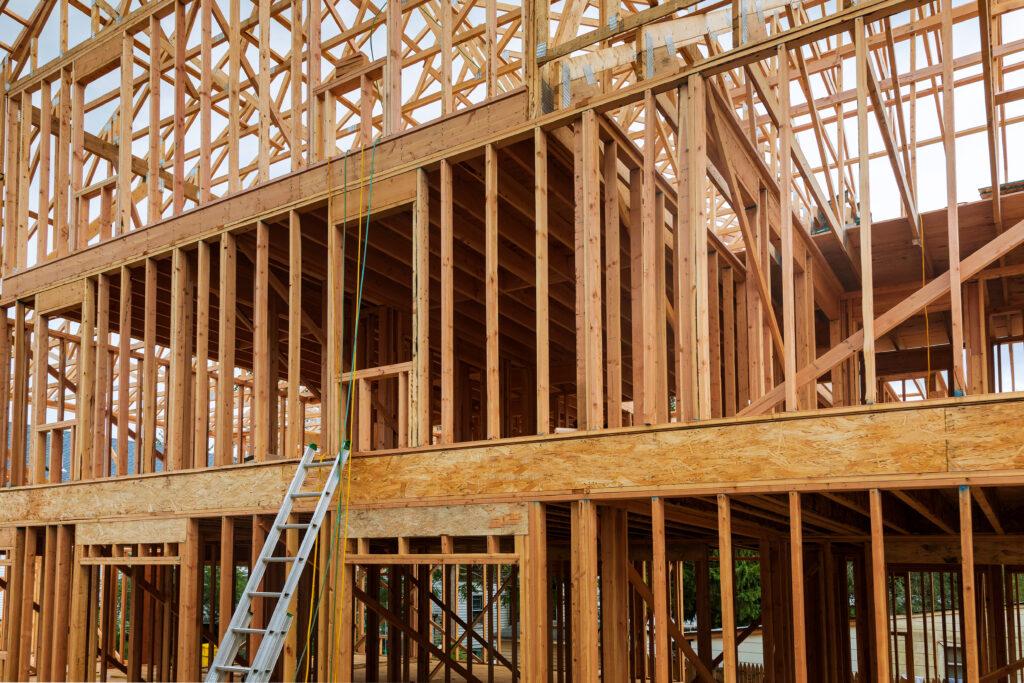
Table of Contents
Introduction to House Framing in Canada
The Importance of Framing in Construction Materials Used in Framing Pre-Construction Planning for Framing
Step-by-Step Process of House Framing by LG Construction
1: Foundation Preparation
2: Floor Framing
3: Wall Framing
4: Roof Framing
Step 5: Final Adjustments and Quality Assurance
Challenges of House Framing in Canada
Building Codes and Regulations for Framing in Canada
Energy Efficiency Considerations in Framing Why Choose LG Construction for House Framing
Conclusion
1. Introduction to House Framing in Canada
House framing is the process of constructing the skeletal structure of a house, which includes floors, walls, and roofs. It’s a critical phase in building any home, laying the foundation for all other stages of construction, from insulation to wiring to finishing touches.
Canada’s unique climate necessitates robust construction techniques to withstand extreme weather conditions. The country sees heavy snowfall, icy winters, and frequent rain in many regions. LG Construction, known for its craftsmanship and attention to detail, has developed specialized framing methods that cater to these environmental challenges while ensuring durability and comfort for homeowners.
2. The Importance of Framing in Construction
The frame of a house is more than just its skeletal structure; it is the backbone that gives the home shape, strength, and stability. Proper framing ensures that:
Structural integrity is maintained throughout the house’s lifetime, providing a solid base for floors, roofs, and walls.
Alignment and balance are achieved, preventing issues such as sagging floors or crooked walls.
Safety standards are met, especially in areas with potential natural hazards such as earthquakes or heavy snow loads.
LG Construction emphasizes the importance of a well-constructed frame. A sound frame supports not just the physical structure but also the internal systems of a house, such as wiring, plumbing, and HVAC. Poor framing can lead to problems like water leaks, air infiltration, and even long-term structural damage, which is why LG Construction takes extra care to ensure that every frame meets the highest industry standards.
3. Materials Used in Framing
In Canada, wood is the most common material used for framing homes, and it has been for centuries. Wood is affordable, easy to work with, and available in abundance. LG Construction primarily uses wood framing due to its durability, flexibility, and sustainability.
Common Types of Wood for Framing:
Spruce-Pine-Fir (SPF): This is one of the most common choices for framing in Canada. SPF is light, strong, and easy to cut and shape, making it ideal for both floors and walls.
Douglas Fir: Known for its exceptional strength and resistance to warping, Douglas Fir is often used in areas requiring extra load-bearing capacity.
Hemlock: Another sturdy option, used particularly in areas where humidity is a concern due to its resistance to moisture.
In some cases, LG Construction also incorporates engineered wood products such as LVL (Laminated Veneer Lumber) and OSB (Oriented Strand Board) for specific parts of the frame, including headers, joists, and roof trusses. These engineered products offer superior strength and uniformity compared to traditional lumber, making them an excellent choice for homes in regions with high wind or heavy snow loads.
4. Pre-Construction Planning for Framing
Before the first nail is hammered into the wood, LG Construction goes through a meticulous pre-construction phase that includes design, material selection, and site preparation. This phase is critical because any errors in planning can result in costly delays and structural problems down the line.
Design and Engineering
The first step in the planning process is to work closely with the architect and structural engineer to design the home. LG Construction’s design team ensures that the plans account for local building codes, energy efficiency requirements, and the specific needs of the homeowner.
Material Procurement
Once the design is finalized, LG Construction sources high-quality lumber and other materials. The company has longstanding relationships with suppliers, ensuring that only top-tier materials are used for framing.
Site Preparation
The construction site is prepared by clearing any debris, leveling the ground, and ensuring proper drainage. Site conditions such as soil type, slope, and local climate all influence the design of the foundation, which in turn affects the framing process.
5. Step-by-Step Process of House Framing by LG Construction
Now, let’s delve into the step-by-step process that LG Construction follows when framing a house.
Foundation Preparation
The first part of the framing process involves laying a solid foundation. In Canada, the type of foundation used often depends on the region. In areas with cold winters, the foundation must be deep enough to avoid frost heave, which can cause structural damage.
Slab-on-grade foundations: This type of foundation is often used in areas where the frost line is not too deep. It involves pouring a single layer of concrete to create a base for the house.
Basement foundations: Common in many parts of Canada, basement foundations offer additional living space and are designed to withstand extreme cold.
Crawlspace foundations: These are used in areas where basements are not practical. A crawlspace elevates the house slightly off the ground and provides easy access to plumbing and electrical systems.
LG Construction ensures that the foundation is level, secure, and properly insulated to avoid issues down the line.
Floor Framing
Once the foundation has been laid and cured, the next step is to start floor framing. This phase involves creating the horizontal structure that will support the walls and roof of the house.
Sill Plates: These are horizontal pieces of lumber that are anchored to the foundation. They provide a base for the rest of the framing to sit on.
Floor Joists: Joists are long beams that span the width of the house and support the floor. LG Construction often uses engineered wood joists for added strength.
Subflooring: After the joists are in place, a layer of plywood or OSB is laid down to create the subfloor. This is the base upon which flooring materials will eventually be installed.
Step 3: Wall Framing
With the floor in place, the next step is to erect the walls. Wall framing is a critical phase, as it determines the shape and dimensions of the house.
Studs: Vertical beams, called studs, are spaced evenly (typically 16 to 24 inches apart) to create the wall structure. These studs are secured between horizontal plates at the top and bottom.
Headers and Cripples: Above doors and windows, special framing elements called headers are used to bear the load. LG Construction ensures that each opening is properly framed to prevent sagging or misalignment.
Exterior Sheathing: Once the walls are framed, LG Construction installs a layer of sheathing to add rigidity to the structure and provide a surface for attaching the exterior cladding. Sheathing also serves as the first line of defense against wind and moisture.
Step 4: Roof Framing
Roof framing is the final stage of constructing the house’s skeleton. The roof must be sturdy enough to support the weight of snow, withstand high winds, and keep out rain.
Trusses or Rafters: Roofs are typically framed using pre-fabricated trusses, which are strong, triangular frames that distribute the weight evenly. In custom designs, LG Construction may opt for rafters, which offer more flexibility in design but require more on-site labor.
Roof Sheathing: Once the trusses or rafters are in place, the roof is covered with plywood or OSB sheathing to create a solid base for the roofing material.
Roof Underlayment: A layer of waterproof material is applied over the sheathing to protect the house from moisture.
Step 5: Adjustments and Quality Assurance
Before moving on to the next phase of construction, LG Construction conducts a thorough inspection of the frame. Any necessary adjustments are made to ensure that everything is square, level, and properly secured.
6. Challenges of House Framing in Canada
Framing a house in Canada comes with unique challenges that builders must address to ensure the longevity and performance of the structure. Some of the most common challenges include:
Weather Conditions
Canada’s harsh weather can pose significant challenges during the framing process. Cold winters, heavy snowfall, and frequent rain require builders to be vigilant about moisture management. LG Construction often uses techniques like temporary shelters or tarps to protect the frame from rain and snow during construction.
Thermal Bridging
Thermal bridging occurs when heat transfers through materials that are not well-insulated. This can lead to energy inefficiency and increased heating